The HELMETH project
A highly efficient Power-to-Gas process has been realized by the European research project HELMETH. It has the potential to be the most efficient storage solution for renewable energy utilizing the existing natural gas grid without capacity limitations and to be a source for “green” Substitute Natural Gas (SNG) to avoid fossil carbon dioxide emissions. The objective of the HELMETH project is the proof of concept of a highly efficient Power-to-Gas process by realizing the first prototype that combines a pressurized high temperature steam electrolysis with a CO2-methanation module. The efficiency is significantly increased by using the heat of reaction from the exothermic methanation reaction to produce steam for the high temperature electrolysis. Since the produced SNG is fully compatible with the existing natural gas grid and storage infrastructure, practically no capacity limitations apply to store energy from fluctuating renewable energy sources (Figure 1). A significant advantage of the HELMETH PtG technology in contrast to PtG plants with low temperature electrolysis modules is its higher efficiency resulting to considerably lower electricity demand per SNG output. The HELMETH consortium consists of the partners Karlsruhe Institute of Technology (coordinator), Politecnico di Torino, Sunfire GmbH, European Research Institute of Catalysis A.I.S.B.L., Ethos Energy Italy, National Technical University of Athens and DVGW-German Technical and Scientific Association for Gas and Water. The research project with a duration of nearly 4 years had a total budget of approximately 4 million euro and was co-financed by the European Union's Seventh Framework Programme for the Fuel Cells and Hydrogen Joint Technology Initiative under the Grant agreement no. 621210.
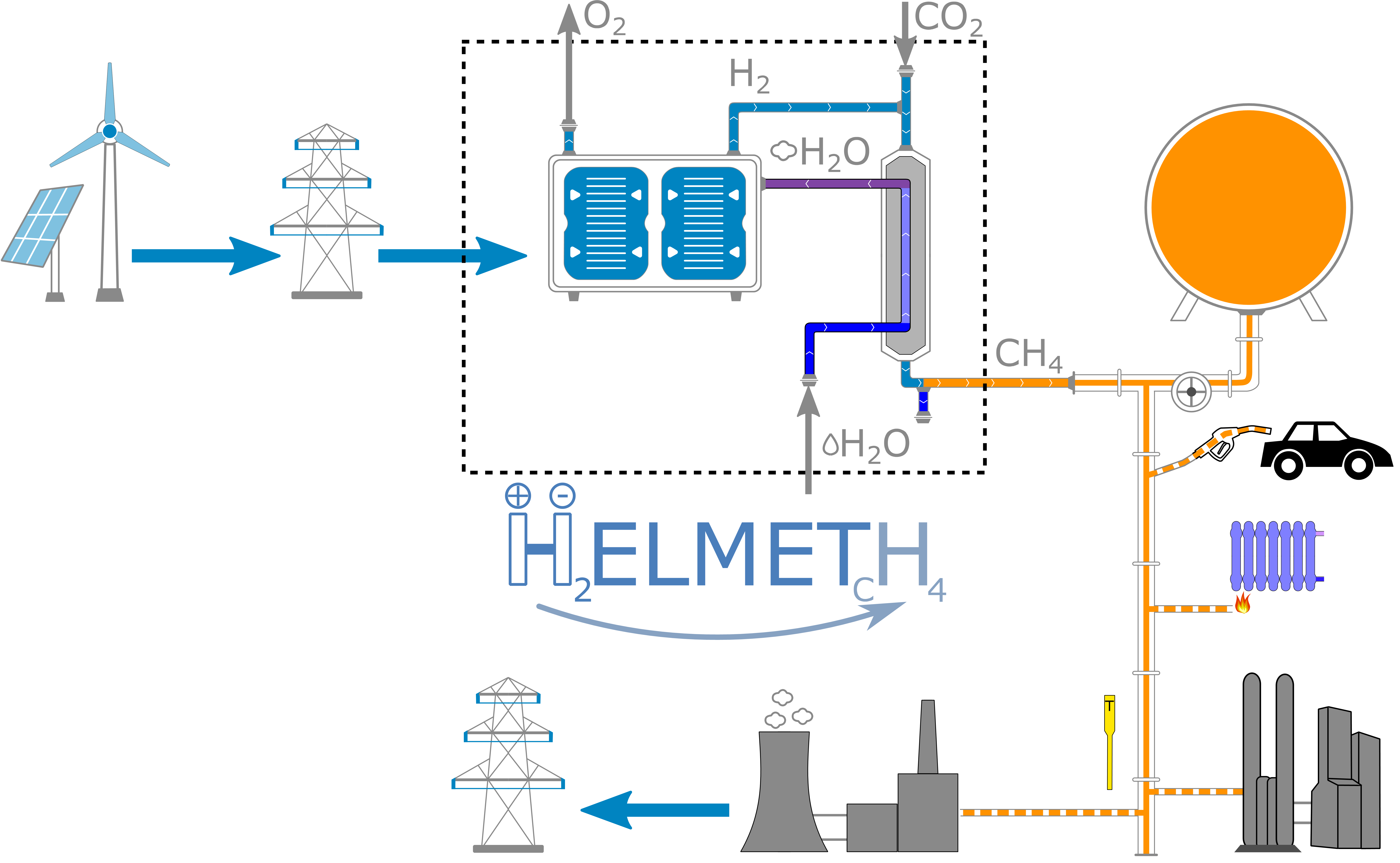
The realisation of the PtG technology as planned within HELMETH needed several development steps and focused on the following objectives, which had to be met in order to show the feasibility of the technology:
- Design and construction of a pressurised electrolysis module including high corrosion resistant and long-term stable heat exchangers
- Design and construction of a multi-step CO2 methanation module that produces SNG which is fully compatible with the existing natural gas grid and storage infrastructure
- Thermal integration of pressurized high temperature steam electrolysis with CO2-methanation
- Demonstration of the technical feasibility of a conversion efficiency > 85 % from renewable electricity to methane, which is superior to the efficiency for the generation of methane or even hydrogen via conventional water electrolysis.
- Elaboration of the conditions / scenarios for an economic feasibility of the PtG process towards methane as chemical storage, without significantly deteriorating the CO2-balance of the renewable electricity.
- Life Cycle Analysis of the overall process and evaluation of the impact of CO2 sources on the system CO2 footprint
Achievements:
At first the European natural gas grid regulations were evaluated in order to specify the overall system requirements and especially the targeted SNG quality criteria. This process was essential for the development of the methanation module, which has to produce SNG that is fully compatible with the existing natural gas infrastructure. Based on the development of the overall system specifications, several PtG integration schemes with different methanation reactor concepts were investigated by detailed process simulation. The consortium chose a multi-step methanation module with a boiling water cooling that is producing saturated steam for the electrolysis module.
Short stack tests of the high temperature steam electrolysis module showed degradation rates below the set target of 0.5 % / 1000 h. The development of high corrosion and high temperature resistant direct laser metal sintered heat exchangers resulted in several prototypes that were evaluated. Further electrolysis stack tests were conducted in co-electrolysis (simultaneous feed of CO2 and Steam) mode and provide a good basis for assessing the potential to produce a synthesis gas for the methanation process. This offers the chance to further increase the overall PtG efficiency.
In order to reach high methane yields in the methanation module, different Nickel and Ruthenium catalysts were tested and optimised. A catalyst with lower Ni concentration and indication of better long term stability was developed. Extensive tests in stand-alone mode were performed with the methanation module in order to characterize its performance. The gas pressure was varied from 10 to 30 bar and a load modulation from 20 to 100 % (60 kW equivalent SNG production at 30 bar and 100 % load). Hereby the boiling water cooling showed an extremely stable and effective heat removal capability, while being able to control the steam temperature accurately. Start-up time of the methanation reactor from hot-standby was in the range of minutes; However it could be significantly reduced in fully automated plants. At the end of the test campaigns the methanation module produced SNG excelling the quality targets by far. For stand-by operation a hot stand-by at the optimum boiling water temperature of 250 °C proved to be most effective.
Finally, both modules were coupled and commissioned at the Sunfire premises. The thermal integration of both units was performed by a steam line from the methanation module to the steam inlet of the electrolyser module and by connecting the hydrogen outlet of the electrolyser to the methanation. The demonstration plant was operated semi-automated in part load. A technical obstacle identified within the HELMETH project, is the need for new technical solutions for accurate steam mass flow control at extremely low volume flow rates at the electrolyser inlet. Since the electrolyser modules operates at pressures in the range of 15 bar, while the differential pressure between the not communicating anode and cathode side should remain well below 100 mbar to avoid stack damage, even small fluctuations in the steam volume flow rate are critical. A further technical challenge is the development of high temperature thermal insulation materials, which maintain their insulation properties at high pressures. Approx. 2.5 % of loss in the overall efficiency was identified to be caused by this reason. An efficiency of the integrated HELMETH Prototype of about 76 %HHV could be achieved. By scaling up the HELMETH concept, parasitic losses could be reduced, resulting in an overall PtG efficiency over 80 %. In addition, a scale up techno-economic study was performed for different renewable energy supply profiles identifying optimum plant sizes and operation strategies.
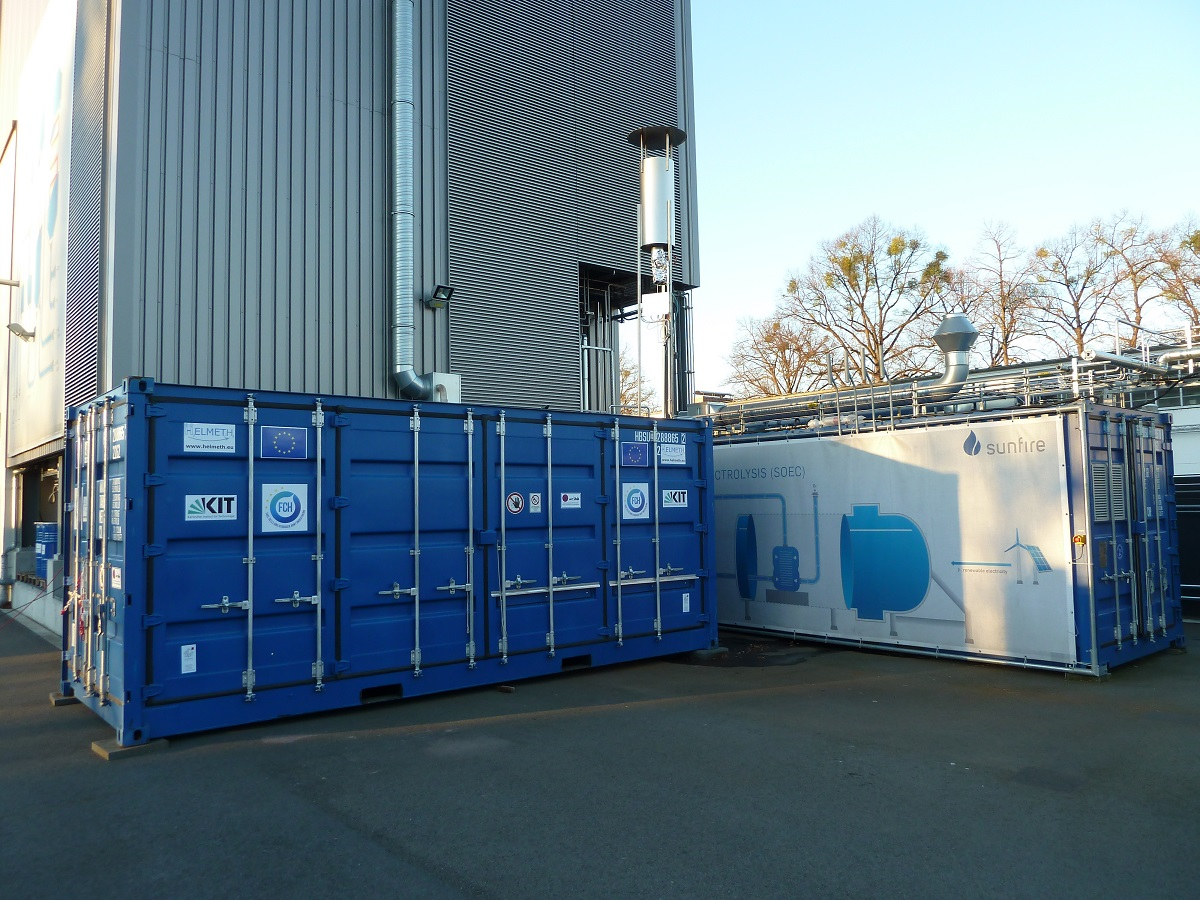
A full-scale Life Cycle Assessment of the overall process against benchmark scenarios was completed, alongside with the evaluation of the impact of CO2 sources on the system CO2-footprint. Business cases for various operation scenarios of the Power-to-Gas units were elaborated and evaluated, while a complete exploitation road map was developed.
Conclusion
The main objective of the project to prove the feasibility of an integrated PtG process for highly efficient storage of renewable energy was achieved. The project showed a successful operation of the worldwide first pressurised high-temperature electrolyser at a multi-stack system level coupled with an innovative methanation unit.
Project website: www.helmeth.eu